A Better Understanding of Aluminum Extrusions
Posted on October 07, 2019 by Admin
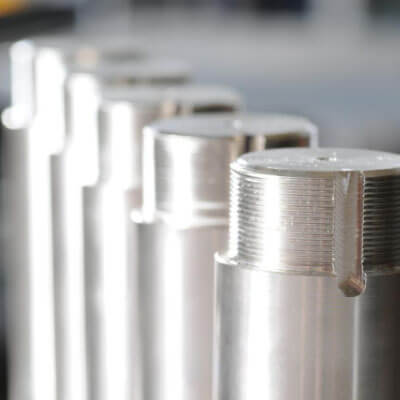
Custom aluminum extrusions undergo a special process whereby an aluminum alloy material is “force-fed” through a custom die to produce a pre-designed cross-sectional profile. It’s actually quite similar to squeezing toothpaste out of the tube.
Aluminum extrusion suppliers produce and deliver finished custom aluminum extrusions. For architects, engineers, and designers, the benefits of extrusions are countless – mainly because of the remarkable flexibility with design specifications.
As for the extrusion die, it’s best understood by comparing the open end of a toothpaste tube. Since the opening is round, the toothpaste comes out as a “round extrusion”. With customized extrusions, shapes, angles, and channels are possible.
Not surprisingly, the use of aluminum extrusions has increased substantially over the last few decades. As more and more end-users realize the many benefits, the global aluminum extrusions market is bound to grow exponentially in the coming years.
Infinite Shapes and Sizes
The aluminum extrusion process allows for the creation of infinite shapes and sizes – everything from the most simple to the most complex. Typically, there are three primary shape categories:
- Solid – extrudes without any openings
- Hollow – extrudes with one or more “voids”
- Semi-hollow – extrudes with partial “voids”
The real beauty of aluminum extrusions is the vast range of applications – from architectural, to automotive, to electronics, to aerospace, to construction. And the design options are endless.
Room Temperature Cooling
After the shearing process, custom aluminum extrusions require additional cooling. At this point, the profile remains intact until the material hits room temperature (a must before the next step).